A Comprehensive Guide To Double Wall Corrugated Pipe Machine
Nowadays, double wall corrugated pipes are widely used in building drainage, municipal drainage, farmland low pressure irrigation and other fields. So, what are the components of double wall corrugated pipe machine? What is the production process? Let us introduce you to it.
What raw materials can the double wall corrugated pipe machine produce?
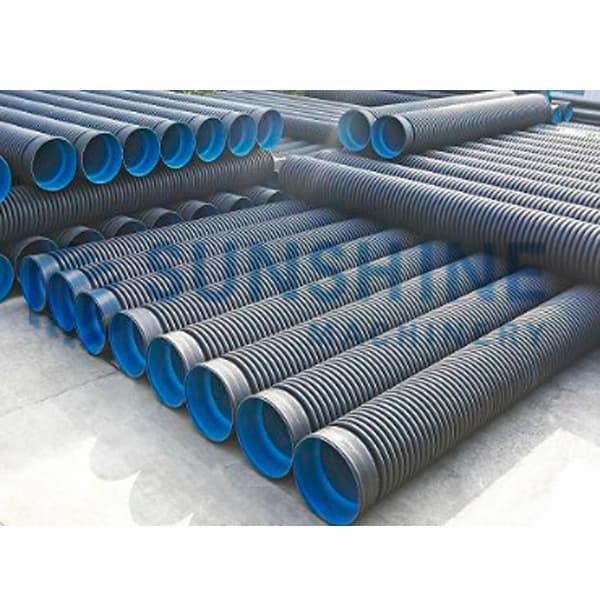
Currently, double wall corrugated pipes on the market are mainly produced with PVC, PP, PE, and HDPE.
What are the components of double wall corrugated pipe machine?

The double wall corrugated pipe machine include extruders, die head, forming machine, haul-off machine, cutting machine, unloading table, etc.
What are the forming methods of double wall corrugated pipe machine?
There are generally two forming methods for double wall corrugated pipes: vacuum forming and inter-wall inflatable forming. Some of these two methods are used simultaneously.
The appearance quality of the tubes produced by the vacuum forming method is good, but the dimensional stability of the inner and outer diameters is poor, and the vacuum holes are easily blocked, causing corrugated defects on the outer wall of the product.
Pipes produced by the inter-wall inflation forming method have good dimensional stability.
What are the production principles and precautions for double wall corrugated pipe machine?
The structure of the double wall corrugated pipe die head is relatively complex. The main feature is that there are two layers of inner and outer flow channels in the same mold. Compressed air needs to flow between the inner and outer flow channels.
The inner sizing sleeve requires a cooling system. At the same time, in order to compensate for the heat loss caused by the passage of cooling water, heating rods are generally required.
In the production of large diameter pipes, double layer co-extrusion technology is also required.
The corrugation forming machine is the core equipment for the production of double wall corrugated pipes. It consists of three parts: the forming module, the transmission system and the control system.
There are two types of corrugation forming machines: vertical and horizontal. The vertical corrugation forming machine occupies a small area and has a compact structure, but it is difficult to replace modules.
The horizontal corrugated forming machine’s forming module opens and closes horizontally and occupies a larger area, but it is much more convenient to replace the module than the vertical type, so it is more widely used.
What should we pay attention to when heating the double wall corrugating machine?
Pay attention to the temperature.
(1) The extruder and mold can be heated to about 1.5×2h.
(2) Part of the mold is evenly grilled at the operating temperature of the burner. Pay attention to uniformity, otherwise the mold and mandrel will be deformed.
(3) Use a blowtorch to heat the module, and then bake it evenly to about 40 degrees Celsius.
Double wall corrugated pipe machine mold adjustment.
The mold can be opened when the temperature is normal.
When opening the mold, run it at low speed first and check whether the mold blank is uniform. If the adjustment screws are uneven, wait until it is uniform.
At the same time, check whether the material temperature reaches the kneading temperature, and stop the machine after a period of time.
Iron wire introduction.
After the material uniformity and kneading temperature are normal, the machine stops working and the iron wire is introduced from the wire trough. The export mold is about 30mm.
Check the air path of the double wall corrugated pipe machine.
Open the manual air valve to see if it is ventilated and check the air pressure.
Adjust the front and rear position of the molding machine.
Push the molding machine to the die opening, close the two pairs of corrugated paper blocks according to the direction, fix the bolts, and check whether there is knocking on the machine head.
Open the double wall corrugated pipe machine.
1.Screw the screw of the air nozzle to the mandrel through the air rod. When tightening the air rod, tighten the air rod from the end of the molding machine.
2. Requires two people to operate. The person in front puts the air nozzle close to the mandrel, and the person behind puts the air rod through the gap of the molding machine, tightens it on the mandrel, and then quickly moves the molding machine to the designated position.
3.Open the main engine, unfold the air valve, pay attention to these actions, be sure to seize the opportunity, remember to pay attention, and then pass the iron wire through the air rod and fix it on the blank. Look at the shape of the product.
4.If the ripples are too full and there are flashes, the air pressure is too high, please adjust the air pressure slightly.
5.Double wall corrugated pipe machine is on the contrary. If no corrugations are formed, it means that the air pressure is too small and the air pressure can only be increased.
6.If the wall thickness of the bellows is too thick, it will speed up the driving speed of the molding machine or slow down the driving speed of the extruder.
7.Conversely, if the bellows is too thin, the molding machine may be driven slower, or the extruder may be driven faster. After normalization, the speed can be gradually increased.
Adjust the windering machine.
When there is an abnormality in the pipe of the double wall corrugated pipe machine, it can be placed on the winding machine for winding. Pay attention to adjusting the winding deformation of the winding machine. Do not overtighten and do not wrinkle or deform.